Hinge Tool
Solution Bulletin
The Problem:
Hinges, a more complex form, may be processed in a punch press. With today’s machine technology—punch presses with stroke control—hinges no longer need to be a headache to produce. By using a hinge tool on the turret press, fabricators can punch many different types of knuckles of different lengths and diameters. Fabricated metal enclosures and similar cabinetry that require hinges can be fabricated with integral hinge knuckles.
The Mate Solution:
Forming a successful hinge in a punch press is a process that typically involves two forming tools, Forming Tool 1 and Forming Tool 2 (also referred to as the “knuckle tool”), and three forming strokes. These forming tools are in addition to standard punching tools used to create the tabs for forming.
- After the tabs have been punched in the sheet to be formed, Forming Tool #1 is used to make the first 2 forming strokes. This first form produces the leading edge of the tab.
- The second forming stroke is added to all tabs to be formed. This forming stroke bends the tab up to a designed angle. The spring loaded lower assembly, or die, pushes the sheet off the lower insert before the sheet advances to the next forming location.
- The final forming stroke uses Forming Tool #2, or the “knuckle tool,” which curls the angled tab to form a hinge. This tool also includes a spring loaded lower assembly to lift the material off the lower insert before advancing to the next forming location.
The benefits of forming hinges in a punch press include: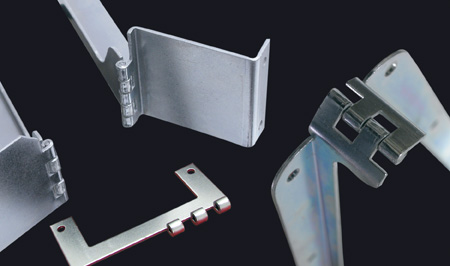
- Eliminates secondary operations that attach hinge components
- Separate hinges, fasteners, spot welds or other assembly operations are no longer needed
- Does away with the cost of specialized press brake or stamping tooling necessary to create hinge forms.
- Ensures greater accuracy over more manual secondary operations.